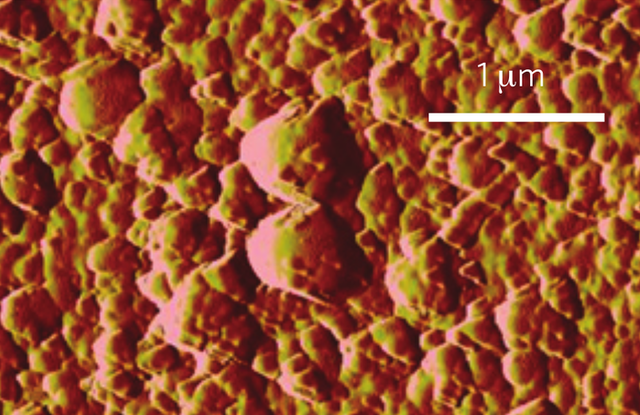
Microscopically, glasses are solids that look more like liquids—they lack a regular crystalline structure. The liquid character is no accident, since a typical glass is made by cooling a fluid rapidly. If done in the right way, this skips the usual crystallization that occurs at the freezing point of the material, leaving a disordered state. If we want to create a glass with specific properties, we need precise control over the fluid-to-glass transition, but that has proven very difficult to achieve in practice.
To this end, Yunlong Guo et al. have developed a way to produce stable glasses made of polymers. As described in a Nature Materials paper published February 5, the resulting glasses are extremely lightweight, have a higher transitional temperature, and maintain their properties up to a higher temperatures than normal glasses. The researchers made the glasses by deposition rather than cooling, using a technique known as matrix-assisted pulsed laser evaporation, or MAPLE. The result is a glass built up of nanoscale globules, a material with interesting theoretical properties as well as potential applications.
The typical way of creating glass involves starting with a liquid, then quenching it, or cooling it rapidly past its usual freezing point. As a result, the material retains some of its liquid characteristics even as it solidifies. This process comes with a cost: the transition from liquid to glass is a kinetic process, and depends on the specific rate at which the glass is cooled. Even more, rapidly cooling the liquid doesn't dramatically change its glass transition temperature, so it's hard to create glasses that are stable at high temperatures.
The MAPLE technique begins with a frozen solution of poly(methyl methacrylate), or PPMA, the polymer researchers wish to make into a glass. The solution is subjected to a pulsed laser, which blasts some of the polymer free, and deposits a film of it onto a silca substrate. The film is made up of nanoscale globules, with sizes that depends on the glass transition temperature: higher temperatures result in a smoother film. Above the glass transition temperature, the globules go away entirely.
Compared to rapid quenching of PPMA, MAPLE produces a glass with a significantly higher transition temperature (about 40°C hotter), meaning the same material is stable at higher temperatures. Using index of refraction measurements, the researchers also determined the glass to be about 60 percent of the density achieved using other techniques, meaning it's a much lighter weight material. Despite the significant reduction in weight, the MAPLE-deposited PPMA showed no substantial loss in rigidity: the lighter glass is as strong as glasses produced using quenching.
The MAPLE-deposited PPMA can be made into a standard PPMA glass by heating itrapidly, then cooling again, and this causes the globules to shrink and even out. Because of this and the temperature dependence of the roughness, the researchers believe there is a deep connection between the globule structure and formation of the film. Normally, the disorder in a glass is on the molecular scale, but the globules seem to act as (relatively) giant molecules, so the glassy structure is exhibited on the nanometer scale.
The relatively lightweight and thermally-stable glasses produced using MAPLE deposition should make them useful in a wide variety of applications. In addition, because the globules are made up of polymers, these glasses are a hybrid: on the molecular level, they are polymer, but on the nanometer scale, they resemble standard glasses, which may lead to new theoretical understanding of glassy materials.
Nature Materials, 2012. DOI: 10.1038/nmat3234 (About DOIs).
Listing image by Photograph by Rod Priestley, Princeton University
reader comments
14