Knitting and baking the cars of the future
- Published
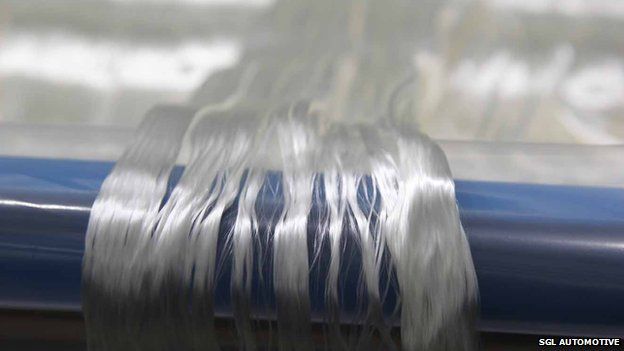
Rising skywards like tinsel on a Christmas tree, the white polyacrylic yarn slowly unfolds from dozens of vast wooden crates, each containing 43 kilometres of material.
Gentle tension pulleys help keep the soft, silky material straight without snapping it as it is stretched from floor to ceiling, then through into the next room to undergo a process of oxidation.
"It's changing colour," says factory manager Steve Swanton. "That's the first reaction."
Side by side, dozens of thin threads slowly wind their way up a series of heated rollers, gradually changing from white, to silver, to gold, then copper, and finally black.
"We're not adding anything here," says Mr Swanton. "We're just cooking the material."
'Paradigm shift'
But this not a textiles factory.
What is cooking here is carbon fibre - a strong, lightweight material widely used in industries such as Formula 1 or aerospace and defence, and one that could soon be put to good use by the automotive industry.
"All the lingo in carbon fibre is based on textiles," grins Mr Swanton. And like the cotton mills of the past, SGL Automotive Carbon Fibers' newly built factory in Moses Lake, Washington State, could deliver an industrial revolution of its own.
The process of stabilising and making the material fire proof is done in four 50 metre long ovens, each hotter than the last one with temperatures rising from 200 to 1,100 degrees Celsius.
As oxidation levels increase, the strips of material change appearance. As they exit at the far end of the factory they resemble giant spools of old-fashioned audio tapes.
The strips then feed through into two furnaces, one low- and one high-temperature, each the height of a tall man and covering an area the size of a badminton court.
Here a carbonisation process chemically removes all non-carbon molecules while also changing the bonding of the carbon molecules. The result is ultra-strong carbon fibre, which is spooled onto large cardboard bobbins that are stacked onto pallets, each containing 2.7 kilometres of this hugely flexible, strong and light material.
"The way we do things here marks paradigm shifts, both in the carbon fibre market and the automotive market," Mr Swanton says.
Cheaper solution
Carbon fibre is made from thin threads that each contain a number of carbon filaments. The Aerospace industry generally uses 3K or 6K strands, which have 3,000 or 6,000 carbon filaments per thread. But this is very expensive, so to cut costs SGL Automotive uses threads with 100,000 strands.
One major difference, beyond cost, is that the 100K strands are more difficult to handle and shape. The manufacturer gets around this by laying down the carbon in just one direction rather than weaving carbon strands into cloth.
"We are not producing a woven fabric," says Dennis Bauman, head of business development at SGL Automotive. "That's for aeroplanes and for super-sports cars and it's really expensive."
Instead, the carbon fibre is shipped to SGL Automotive's German factory in Wackersdorf, where a thermoplastic material is injected to bind them together into reinforced plastic sheets. Multi-directional strength is achieved by layering the sheets with the fibres pointing in different directions before they are moulded into shape.
German carmaker BMW - SGL Automotive's only customer and owner of 49% of its shares - uses the material to produce body parts for the main cabins of its futuristic plug-in models i3 Megacity and i8 sports car, which will hit the road in 2013 and 2014.
The i3's cabin will be made from just 35 carbon fibre parts, which simplifies the manufacturing a great deal when compared with similarly-sized conventional cars that would require some 500 alloy steel parts to achieve similar results.
"The carbon fibre reinforced plastic parts are at least 30% lighter than aluminium and 50% lighter than steel for identical component use, so the vehicle weighs 300kg less than an ordinary vehicle," Mr Bauman explains.
"We are pretty convinced that this is the future of the automotive industry.
Head start
SGL Automotive's existence is based on such a conviction. The plant was built in late 2010 and early 2011 to guarantee BMW sufficient supplies of carbon fibre at a price that would give it a competitive advantage.
Currently, the Moses Lake factory has capacity to deliver 3,000 tonnes of carbon fibre per year, which is equivalent to 8% of world production, though it could easily expand to produce twice that, according to Mr Bauman.
"We are the first to industrialise carbon fibre to mass produce cars," he says.
"In fact, four or five players dominate about 80% of the world's carbon fibre production, so the only way for BMW to make sure it has enough is to make it themselves - which is why they linked up with SGL to create this joint venture."
BMW reckons as a result of its joint venture with SGL Group, it has stolen a 3-5 year march on the competition.
"We believe carbon fibre has much more use in the future, but making cars in high volume out of carbon fibre is definitely not as easy as people assume it to be," says Ian Robertson, BMW Group's head of sales and marketing.
"The technology that's developed here will ultimately be available for other companies too - but we'll have it first."
Making electric mobility work
Getting involved in the manufacture of the carbon fibre has also made it possible for BMW to address a common concern about carbon fibre, namely that it is such an energy intensive process to make it, that any weight savings and efficiency improvements achieved are quickly cancelled out by the pollution from the manufacturing process.
"By making the carbon in Moses Lake, we can reduce the carbon footprint of the manufacturing process by 50% when compared with buying carbon fibre in the market place," says Manuel Sattig, a spokesman for BMW's i-division, which focuses on new transport and automotive technologies.
"Consequently, the carbon footprint of the i3 will be a third of an equivalent, very efficient car in this segment - if it is powered by the current energy mix.
"That rises to 50% if it is powered by electricity created using only renewable energy."
This is not because SGL Automotive's plant uses any less energy than any other carbon fibre plant. On the contrary, "the oxidation fans draw a lot of energy so we're a big energy consumer", acknowledges Mr Bauman.
Instead, it results from its location, just a few miles away from a huge hydro power plant.
"The main reason why we went to Moses Lake was to get reliable energy from renewable sources," Mr Bauman says. "But in addition, the energy costs are much, much, much, lower than in Germany. Here we pay about 2 US cents for 1KwH, whereas in Germany we pay 15 eurocents per KwH."
In addition, BMW is making the chassis of its i3 and i8 models from recycled aluminium or aluminium produced with renewable energy, and off course the carmaker has no need for the highly energy intensive process of pressing steel for car bodies.
True, SGL's Mr Swanton acknowledges, it is impossible to make cars without producing any pollution at all, but at least, he says, this process pollutes less than conventional methods using steel or aluminium.
"Besides," adds BMW's Roberson, "we need to have a way to bring down the weight to reduce the battery requirements of electric cars.
"Carbon fibre is the material that'll really make electric mobility work."